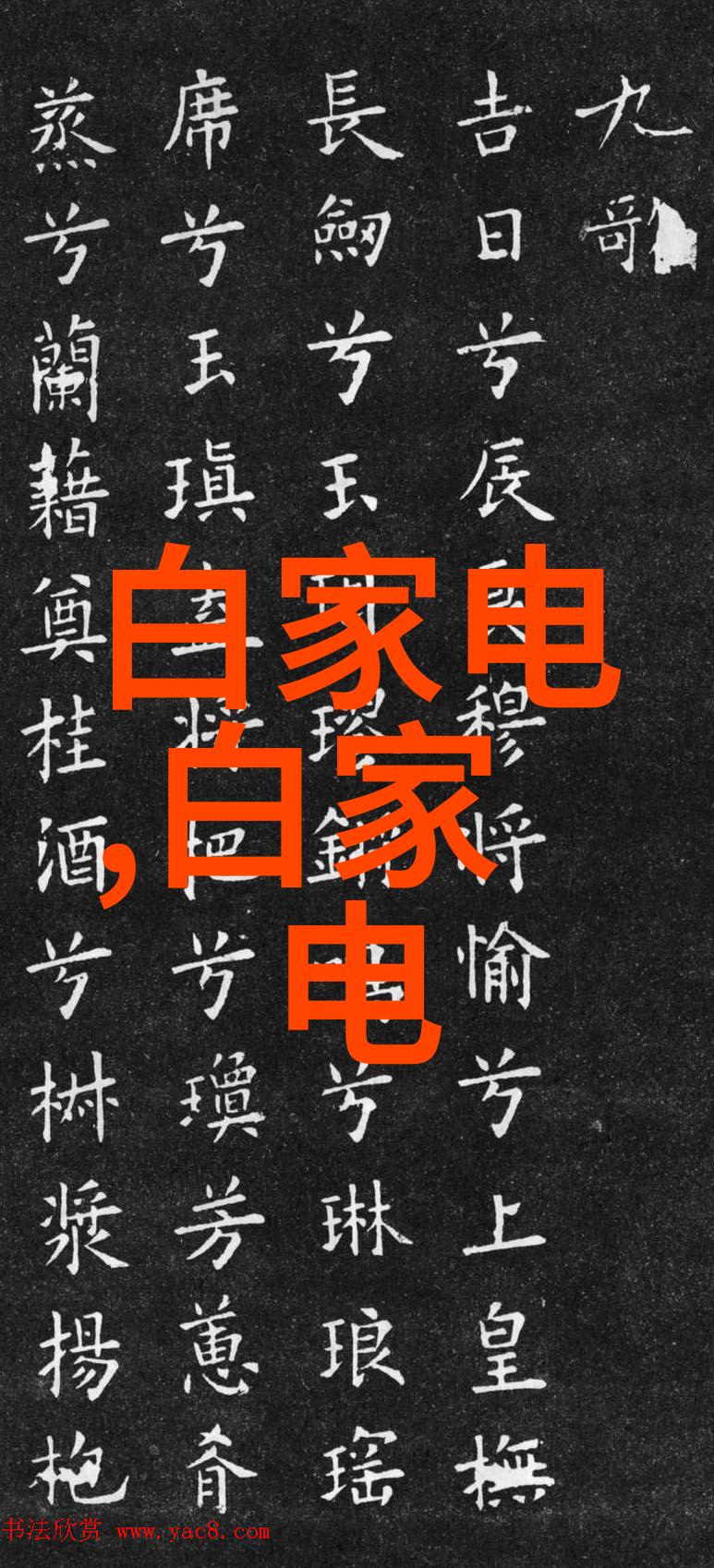
探究Aspen软件中的固定床反应器模型了解和应用
探究Aspen软件中的固定床反应器模型:了解和应用
在化学工程领域,模拟和优化工业过程是提高生产效率和产品质量的关键。 Aspen Plus 是一款广泛使用的化学处理流程设计软件,它提供了多种模拟工具来帮助用户理解复杂的物理和化学现象。在这些工具中,固定床反应器(Fixed Bed Reactor)是一个非常重要的组成部分。
fixed bed reactor aspen是什么
fixed bed reactor aspen是一种常见的催化剂固体载体与气体或液体混合物接触进行化学反应的一种装置。它通常用于大规模制备高分子材料、有机合成、燃料加工等行业。fixed bed reactor aspen在Aspen Plus软件中的实现依赖于其内置模型,这些模型能够准确地描述催化剂颗粒之间以及催化剂与流动相之间的交换特性。
使用aspen plus fixed bed reactor model进行chemical reaction simulation
在Aspen Plus中,用户可以通过设置具体条件如温度、压力、流速等参数来建立一个基于数学方程式的fixed bed reactor模型。这一模型能够模拟不同类型化学反应发生时所需的催化剂量,以及最佳操作条件。此外,该模型还能预测产品分布情况,从而为实际生产提供参考。
Aspen plus fixed bed reactors for different types of reactions
Fixed-bed reactors are suitable for a variety of chemical reactions, including catalytic cracking, hydroprocessing, and synthesis gas production. In Aspen Plus, users can select appropriate models based on the specific reaction mechanism and desired outcome. For example, the Langmuir-Hinshelwood model is commonly used to describe heterogeneous catalytic reactions.
Designing an optimal fixed-bed reactor in aspen plus software
One of the key benefits of using Aspen Plus is its ability to optimize process design through rigorous simulations and sensitivity analyses. By varying parameters such as catalyst particle size distribution or fluid flow rates within predetermined bounds, engineers can identify optimal operating conditions that maximize yields while minimizing costs.
Comparing performance of different types of catalysts in an AspentPlus Fixed Bed Reactor Model
Catalyst selection plays a crucial role in determining the efficiency and effectiveness of a fixed-bed reactor system. In Aspen Plus, users can compare various catalyst formulations based on their activity coefficients, pore volume distributions, and other relevant properties to determine which one performs best under given conditions.
6.aspennetwork analysis for optimizing the operation of a Fixed Bed Reactor Model
The network analysis tool within Aspen Plus allows engineers to visualize complex process flowsheets by breaking down large systems into smaller sub-processes or unit operations like distillation columns or heat exchangers connected with pipes representing material streams flowing between them.
By analyzing these networks engineers can identify bottlenecks in material flow paths potentially causing inefficiencies or even plant shutdowns.
This knowledge enables them to make informed decisions about equipment upgrades maintenance scheduling etc., thereby ensuring reliable operation at minimum cost.