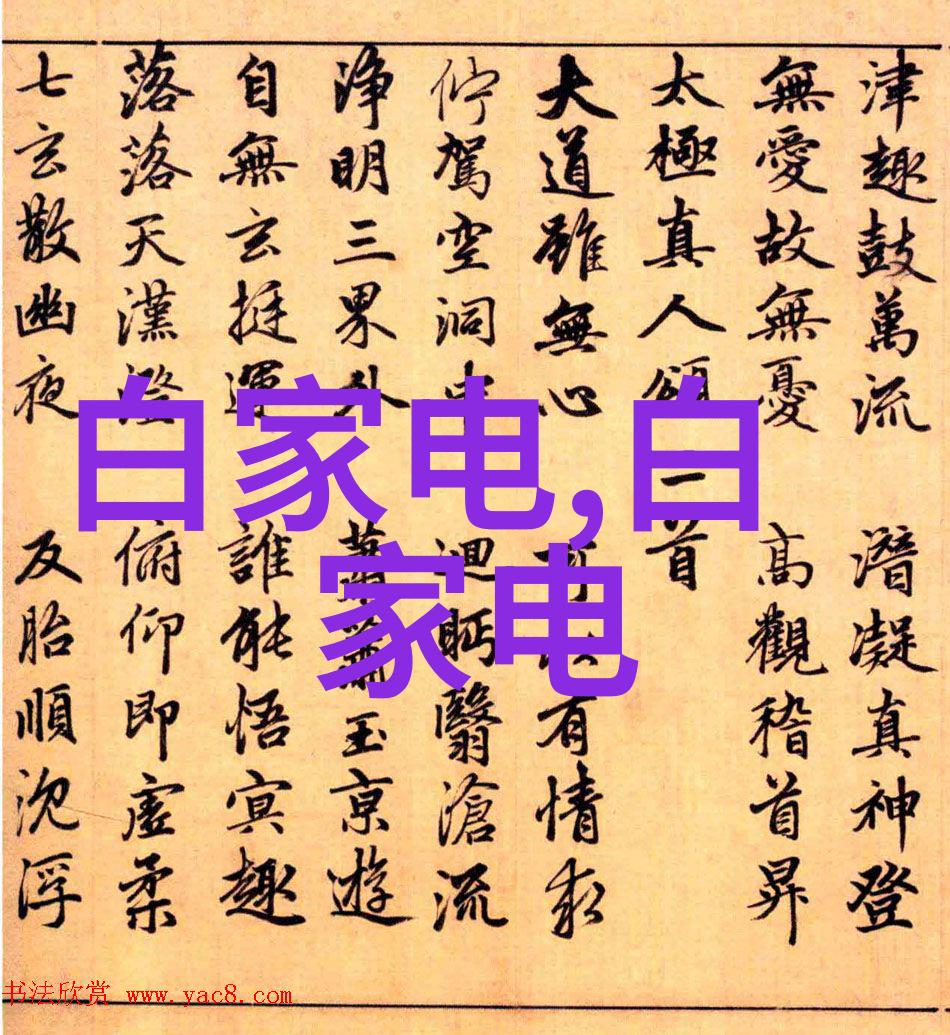
与传统静止型反应器相比动态管式反应器有哪些优势和劣势
与传统静止型反应器相比,动态管式反应器在化学工业中具有诸多优势和劣势,这些特点决定了其在不同应用场景下的使用广泛性和适用性。本文旨在详细探讨这两种类型的反应器之间的差异,以及它们各自所面临的问题。
首先,我们来了解一下动态管式反应器。这种设备通常由一系列连续连接的管道组成,其中每个管段都可以独立进行一定程度的流体混合、加热或冷却等操作。通过精确控制每个管段内流体的速度和温度,可以实现复杂化学过程中的连续生产,这对于提高产品质量和降低生产成本至关重要。动态管式反应器因其灵活性、可控性以及对空间需求较小而受到越来越多工作者青睐。
然而,尽管如此,动态管式反应器并非完美无缺,它们也存在一些潜在的问题。一方面,由于设计复杂,维护成本可能会较高。此外,在实际操作中,如果没有恰当地调节参数,如流量、压力等,那么可能会导致产品质量不稳定或者设备损坏风险增加。而且,由于内部结构复杂,不同部位需要不同的温度控制策略,这就要求操作人员具备更高级别的技术能力。
相比之下,静止型反应器则更加简单直观,它们通常是一种容量大的搅拌罐,其内部配有搅拌棒以确保整个混合物均匀分布。在使用时,只需将所有原料一次性的加入到罐中,然后进行搅拌即可。这使得静止型反应器在很多情况下成为实验室环境中的首选,因为它们易于设置、操作简便,并且一般价格相对较低。
不过,从工业化生产角度出发,静止型反应器存在一定局限性。由于批次处理方式,每次完成后需要清洗整洁工作区,这不仅耗费时间,而且还容易造成污染源产生,因此对于大规模、高效率生产来说并不合适。此外,一旦原料添加错误或搅拌不足,则很难纠正,使得产品质量受影响。
总结来说,无论是动态管式还是静止型,都各有千秋。在选择哪一种作为化学实验或工业生产工具时,我们应该考虑具体任务所需的一系列因素,如试验目的、预期产量、大规模化可能性以及技术支持等。虽然两者各有优劣,但随着科技发展,将来我们仍然期待能够开发出既具有灵活性又能保持稳定性的新一代反应设备,以满足不断变化的市场需求。