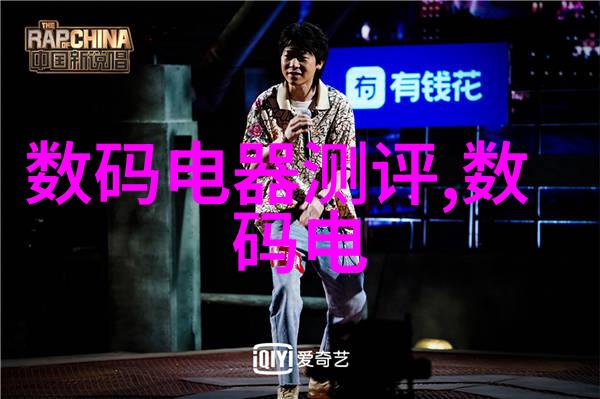
应用层面的挑战如何优化现有的反应器内部结构
在工业生产和化学工艺中,反应器作为一个关键的设备,它们通过各种物理和化学过程来转换原料,生成所需的产品。然而,随着对更高效、更安全、更可持续的操作要求不断提高,对反应器内部构件进行优化变得越来越重要。这些构件包括管道、阀门、泵等,是保证反应器正常运行的基础。
首先,我们需要明确“reaction vessel internal components”这一术语。在讨论这个主题时,我们指的是那些位于或与反应体直接接触到的部件,这些部件能够影响整个反向过程的性能和安全性。它们通常由金属(如不锈钢、铜)、塑料或陶瓷材料制成,以抵抗腐蚀并保持稳定性。
为了理解如何优化这些组成部分,让我们从设计考虑入手。在设计阶段,可以采用计算流体动力学(CFD)软件模拟不同类型组合的情况,从而预测哪种配置会产生最佳结果。此外,还可以利用三维建模技术精确地创建每个部件,并进行交互分析,以评估它们之间可能存在的问题,如粘滞损耗或机械冲击。
一旦选择了最合适的设计方案,就需要考虑材料选择问题。这涉及到耐腐蚀性的考量,因为许多化学物质对金属有强烈的侵蚀作用。如果使用传统材料,那么可能需要额外处理以增强其耐久性;或者,如果采用现代高性能材料,则必须确保成本不会过大地增加。而对于特殊情况,如极端温度或压力的环境下工作,则还需特别注意耐用性的考量。
此外,不同类型的心脏流程控制系统也将影响整体效率。一种常见的心脏流程是热介质循环,这种循环能够有效管理温度差异,同时减少能量消耗。此外,自动控制系统可以帮助调整流量和压力,以实现最佳操作点,并防止因超出范围而导致事故发生。
除了上述硬件方面之外,还有另一种角度值得探讨,那就是软件层面的创新。在数字化转型时代,一些公司已经开始开发智能算法用于实时监控反向运行状态,并根据数据提供即时建议以提高效率。此类算法能够检测异常模式并发出警告信号,有助于预防潜在故障发生,从而提升整体安全水平。
最后,但绝非最不重要的一点是培训与教育。当任何新的技术被引入到现有的操作中时,都必须为员工提供适当的培训,使他们了解新工具、新程序以及如何正确使用它们。这不仅有助于快速融入新变化,也能降低错误发生率,从而进一步提高生产质量和效率。
总结来说,对于想要优化现有反向内部结构的人来说,有几个关键策略可以实施:利用先进设计方法,比如CFD模型,以及最新制造技术,比如3D打印;选择具有足够耐久性且成本可接受的地面材质;采用现代心脏流程控制系统,如热介质循环;加强数字化能力通过智能算法监控设备运行状态,并为员工提供必要训练以确保良好的运作经验。通过这样综合性的方法,可以显著提升反向设备表现,为企业带来长期利益。