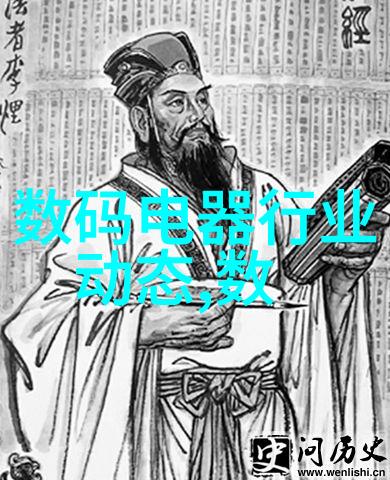
机电一体化有出路吗降低电机损耗的措施有哪些
在探讨机电一体化的可行性时,我们不可避免地会面临一个问题:如何有效地降低电机损耗以提高能效和减少成本。电动机在将电能转换为机械能的同时,本身也消耗了一定量的能源,包括可变损耗、固定损耗和杂散损耗三部分。
首先是可变损耗,这部分与负荷变化相关,主要包括定子铜損(I^2R),转子铜損(I^2R)以及刷片之间摩擦产生的热量。其次是固定损耗,与负荷无关,主要由铁芯磁滞損失和机械磨损所组成,其中磁滞損失随着铁心材料类型而异,而涡流損失则与频率成反比关系。最后是杂散损耗,它包括轴承磨擦、风扇及其他因旋转产生的阻力等。
为了降低这些能源浪费,我们可以采取以下措施:
定子铜損优化:
增加定子的槽截面积,以减少磁路面积并增加齿部磁密。
提高定子的满槽率,可以通过调整绕线尺寸和绝缘尺寸来实现。
减短定子绕组端部长度,可显著降低总体功率因数并提高效率。
转子铜損优化:
减小转子的额外功率因数,以此控制输入电流,并因此减少温度升高。
增大转子的槽截面积以减少额外功率因数。
采用较粗导线和具有较低電阻值材料进行绕组设计,从而进一步节省能源。
铁芯磁滞及其涡流方面改进:
通过调整硅钢片厚度或采用冷轧硅钢板来降低铁芯重量,同时保持性能不下滑。
改进制造技术,如热处理,精加工等,以最小化剩余应力对铁芯性能影响。
杂散方面改进:
(1) 采用更好的绝缘材料,对于确保空载运行中能尽可能减少各种未知来源之间互相作用引起的热量浪费至关重要;
(2) 在设计过程中考虑到整合系统中的各个元件,使得它们能够协同工作以最大限度地降低摩擦、噪音及振动;
(3) 选择合适型号或者专门设计用于特定的应用场景;
风摩方面改进:
(1) 设计更加紧凑但不会导致过热的问题;
(2) 使用更高效且耐用的轴承;
(3) 精心选配润滑剂,并确保润滑系统按需工作;
综合上述措施,不仅可以提升整个设备效率,还能够延长使用寿命并减轻维护压力,从而使得机电一体化成为现实。此外,这些策略对于新产品研发也具有指导意义,有助于开发出更加节能环保、高效稳定的设备。